Compressed air is a crucial component in many industrial processes, powering everything from pneumatic tools and machines to robotic arms and conveyor systems. But like any other utility, it must be managed efficiently and monitored carefully to ensure optimal performance and prevent potential problems.
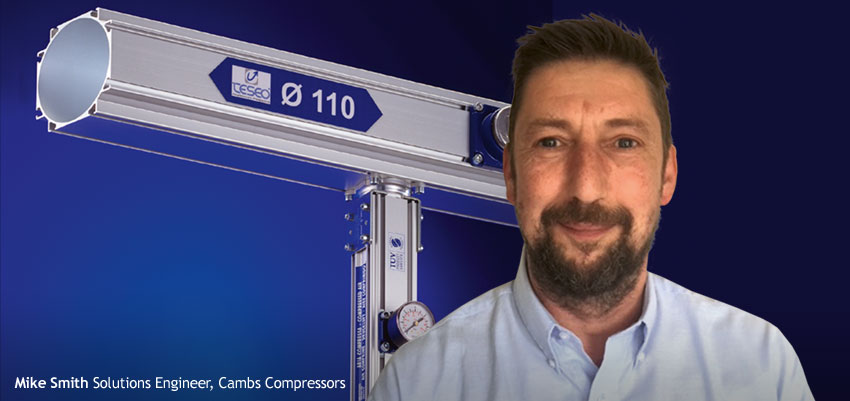
To achieve this, compressed air line fittings and compressed air quality monitoring are critical tools that allow businesses to track and control their compressed air usage and maintain the air quality required for their operations.
Compressed Air Line Fittings
Compressed air line fittings are the connection points that allow compressed air to flow safely and efficiently from one point to another. They come in a variety of materials, sizes, and configurations, depending on the specific application and system requirements.
Common types of compressed air line fittings include:
- Quick-connect fittings: These are used for fast, easy connections and disconnections between hoses, tools, and systems.
- Brass fittings: Brass is a popular material for compressed air line fittings due to its durability, corrosion resistance, and affordability.
- Stainless steel fittings: Stainless steel is a high-performance material that is often used for compressed air applications that require high-pressure, high-temperature, or corrosive resistance.
- Push-to-connect fittings: These are designed for easy installation and require no special tools or skills. They are ideal for DIY or home-based compressed air systems.
Compressed air line fittings must be selected based on a variety of factors, including the required flow rate, pressure, and temperature, as well as the type of air compressor being used and the materials being conveyed through the system.
Proper installation and maintenance of compressed air line fittings are critical to prevent leaks, reduce energy waste, and ensure safe and reliable operation over time.
Compressed Air Quality Monitoring
In addition to proper fittings, it is also essential to monitor and maintain the quality of compressed air used in industrial processes. Contaminated or low-quality compressed air can lead to equipment failure, reduced productivity, and even health hazards for employees.
Compressed air quality monitoring involves measuring and tracking various parameters, such as:
- Moisture content: Excessive moisture can cause corrosion in the air system, leading to equipment failure and reduced efficiency.
- Oil and particulate levels: Contaminants such as oil, dust, and debris can damage equipment and cause premature failure.
- Gas content: Some applications, such as food processing or medical equipment, require compressed air with specific gas content levels to ensure product quality and safety.
Many different types of compressed air quality monitoring systems are available, ranging from simple handheld devices to advanced sensors that provide real-time analysis and reporting.
One of the latest innovations in this field is the Sigma Sensing Compressed Air Quality and Consumption Monitoring System. This system uses advanced sensors and proprietary software to measure and track critical parameters related to compressed air quality and usage, allowing businesses to optimize their operations and reduce costs.
Benefits of Compressed Air Line Fittings and Compressed Air Quality Monitoring
Investing in high-quality compressed air line fittings and regular compressed air quality monitoring can offer a range of benefits for businesses, including:
- Increased efficiency: Proper fittings and monitoring can help to reduce compressed air leakage, leading to improved system efficiency and lower energy costs.
- Longer equipment life: By reducing wear and tear on equipment, businesses can extend the useful life of their compressed air systems and avoid costly repairs or replacements.
- Improved product quality: Maintaining clean and reliable compressed air can help to ensure product consistency and quality, particularly in industries such as food processing and medical devices.
- Enhanced safety: Proper fittings and monitoring can help to reduce the risk of accidents, such as air hose blowouts or overpressure events.
Conclusion
Compressed air is a critical utility in many industrial processes, but like any other resource, it must be managed effectively to ensure optimal performance and safety. By investing in high-quality compressed air line fittings and regular compressed air quality monitoring, businesses can improve efficiency, reduce costs, and maintain safe and reliable operations over time.